Maintenance Tips for Iron and Steel Industry Equipment
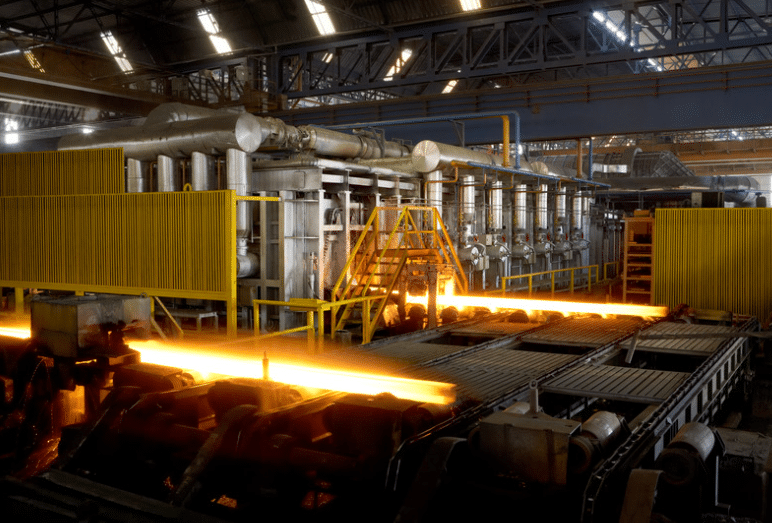
Heavy metal equipment constructed from iron and steel thrives through proper maintenance because neglect enables rapid degradation due to rust damage, regular wear, and mechanical breakdowns. Investing in routine maintenance activities leads to longevity, operational efficiency, and safety standards. These necessary guidelines will help you preserve your heavy metal industrial equipment.
Regular inspections should identify rust
Rust affects iron and steel structures so severely that it causes diminished structural strength and results in expensive maintenance expenses. Inspections should take place routinely to detect corrosion before damage occurs. Protective coatings, including paint, powder coatings, and rust inhibitors, successfully extend metal protection by decreasing oxidation rates and moisture effects.
Regular cleaning to prevent corrosion
Heavy rust occurs faster on iron and steel because of exposure to dirt, grease, and moisture. Real protection from corrosion can be achieved by routinely cleaning equipment with industrial degreasers and rust-preventing sprays. Thoroughly inspect every crevice and operating section of the equipment to remove dowry materials that could lead to future mechanical failures.
Proper lubrication of moving parts
Wear and tear in heavy machinery primarily occurs due to friction. Equipment maintenance requires proper lubrication to achieve smooth operation of its moving components. High-quality lubricants that align with manufacturer recommendations can minimize component friction and prevent overheating. They can also boost the operational timeframe of bearings, gears, and chains.
Monitoring and replacing worn-out parts
The natural degradation of parts will eventually overcome all equipment maintenance efforts. Parts that endure breakdowns past their critical points will cause more extensive damage and lengthy equipment downtime.
Monitoring equipment wear patterns while replacing potential failure points such as gears, bearings, and seals leads to time-efficient cost savings. Companies like Kor Pak, which specialize in high-quality equipment parts, can provide reliable replacements to keep your machinery running efficiently.
Regular bolt and fastener tightening
Heavy industrial work generates vibrations, which eventually lead to disconnection between bolts and fasteners. Loose equipment components result in equipment misalignment as well as increased equipment loads, which poses safety risks. Checking bolt tightness and inspecting component strain levels during scheduled maintenance helps stop equipment failures and enables proper equipment functioning.
Routine inspection and maintenance checks
Regular maintenance detects small problems before they become extensive system failures. It gives operators the opportunity to detect weakened elements, loose connections, and structure damage at an early stage. Checklists during inspections eliminate component oversight while increasing operational efficiency and safety.
Proper storage and environmental protection
Heavy equipment must be properly stored when not in operation to shield it from outside weather elements. Storage beneath a shelter or in an environment with climate control protects machines from destructive high temperatures and moisture. It also shields them from environmental damage which leads to corrosion and destruction.
Training operators for proper equipment use
The way operators handle industrial equipment significantly impacts its operational lifespan. Machines require operator training that includes performance guidelines, weight management rules, and safety emergency protocols. Too much weight and improper use accelerates equipment damage and raises the possibility of mechanical failure.
The takeaway
Heavy metal industrial equipment needs continuous proactive maintenance through regular cleaning, lubricating, rust prevention, and correct operational practices. Such maintenance approaches allow businesses to extend equipment longevity, which results in operational efficiency and reduced repair expenses.